Company Name | Contact Info | Location | ||||||||||||
---|---|---|---|---|---|---|---|---|---|---|---|---|---|---|
İNAN GERİ DÖNÜŞÜM SİSTEMLERİ A.Ş.
KAVAKLI İSTİKLAL MAH. 5006. SOK. NO: 9 PK: 34596 / SİLİVRİ / İSTANBUL / TÜRKİYE
|
Contact Info: +90 533 381 7170
|
Hall: 11
Stand: 1110
|
||||||||||||
Product Groups | ||||||||||||||
|
- Company Info
- Products
- Represented Companies
- Company Brands
İNAN MAKİNE continues to bring innovation to the Recycling Industry with its half-century experience. SINCE 1962 15.000 m2 CLOSED AREA 90 MASTER STAF EXPORT TO 67 COUNTRIES IN 5 CONTINENTS We bring innovation to the plastic recycling industry INAN MAKINE started its first production in a small workshop in Levent Industry area in 1962, it has been producing plastic size reduction machines and recycling washing, drying, extrusion systems needed by national and global plastic manufacturers and recycling companies in its factory which has 15.000 m2 closed area. Inan Makine has strengthened its position with its service quality, customer satisfaction, finding modern and technological solutions to meet the changing needs and expectations of its customers, timely intervention to problems, training and technical services we provide after sales, as well as the guarantee and trust we have provided. With the pride of leaving behind half a century in the production of these recycling machines, İnan Makine has become an assertive name in the sector and positioned among the best quality manufacturers and continues to offer the solutions needed by the plastics industry without sacrificing quality and principles with its expert staff, manufacturing power, machinery and production technologies. MACHINES AND SYSTEMS MICRONIZING MACHINES, CRUSHING MACHINES, SHREDDERS, WASHING SYSTEMS, DRYING SYSTEMS, GRANULE EXTRUSION SYSTEMS, TRANSPORT AND STORAGE SYSTEMS. RECYCLING SYSTEMS PET/PET-E BOTTLE AND SHEET WASHING LINE HDPE/PP WASHING AND GRANULE LINE (BOTTLE, CAP, DRUM, BARREL, etc ) (3D - RIGID PLASTICS) LDPE/LLDPE/PP WASHING AND GRANULE LINE (NYLON/STRECH FILM, BIGBAG/SACK, etc ) (2D - SOFT PLASTICS) OUR ACTIVITY AREAS Large Volume Wastes Industrial Wastes Plastic Barrels Plastic Cases Plastic Pallets Plastic Extruder Scraps Plastic Film Materials Cable And Computer Scraps Textile Products Paper and Cardboard Wood Aluminium, Copper All kinds of plastic pipe, profile, sheet, copper, scrap, rope, sack, nylon, carboy, pet and hdpe bottle, etc size reduction and recycling of plastics washing, drying, extrusion systems we provide with the technology we produce.
Granulator machines are manufactured to recover waste of various sizes and weights. Operating costs and hourly energy costs are at the lowest level. Precautions have been taken to ensure operator safety during operation and maintenance. 5 and 7 rotary rotor blade applications are available. For operation in operator area, cabin application is done with special sound insulation material. It is suitable for crushing the second step of broken parts after pre-fracturing. For easier feeding, the machine can be placed in the pit. Cleaning is very easy in color changes and material changes. High capacity is achieved by special rotor construction.
The thermoform granulator machines are extremely compact and can be placed at the end of the line and work in perfect synchronization with the thermoforming machine. This machine can granulate the PP, PS and PET plates that used in thermoforming process without any interaction. For operation in operator area, cabin application is done with special sound insulation material. Crushing of the plate up to 120 cm width can be carried out. It is possible to operate at variable speeds.
Heavy duty crushers are ideal for daily applications in the plastics processing industry. Ideal for breaking large parts, injection products, blow molding products, thermoform shrinks and coils. Its compact structure makes it easy to access. Cleaning is very easy in color changes and material changes. High capacity is achieved by special rotor construction. The bearings are separated from the crushing zone by the outwardly placed bearings. At this point no dust can penetrate into the bearings and grease will not enter. The body and sieve are opened with a hydraulic cylinder. Transportation and replacement of blades and screens are done in a short time. 3, 5 and 7 rotary rotor blade applications are available.
Cleaning is very easy in color changes and material changes. High capacity is achieved by special rotor construction.The bearings are separated from the crushing zone by the bearings placed outside. At this point no dust can penetrate into the bearings and grease will not enter The body and sieve are opened with a hydraulic cylinder. Transportation and replacement of blades and screens are done in a short time. 5 and 7 rotary rotor blade applications are available. Operating costs and hourly energy costs are at the lowest level.
Micronize machines with disc are high speed fine grinders for micronizing various materials. Micronize machines with disc for brittle plastics such as PE granules and rigid PVC.The plastic material is dosed to the micronizing machine from the center.The plastic material is ground between the rotating disk and the stationary disk. The resulting material is transferred to the cyclone with the fan. Waiting time for plastic material between discs is very short. There is not much heat left on the material.The setting of the discs is done from outside the body. It is easy to change the discs.
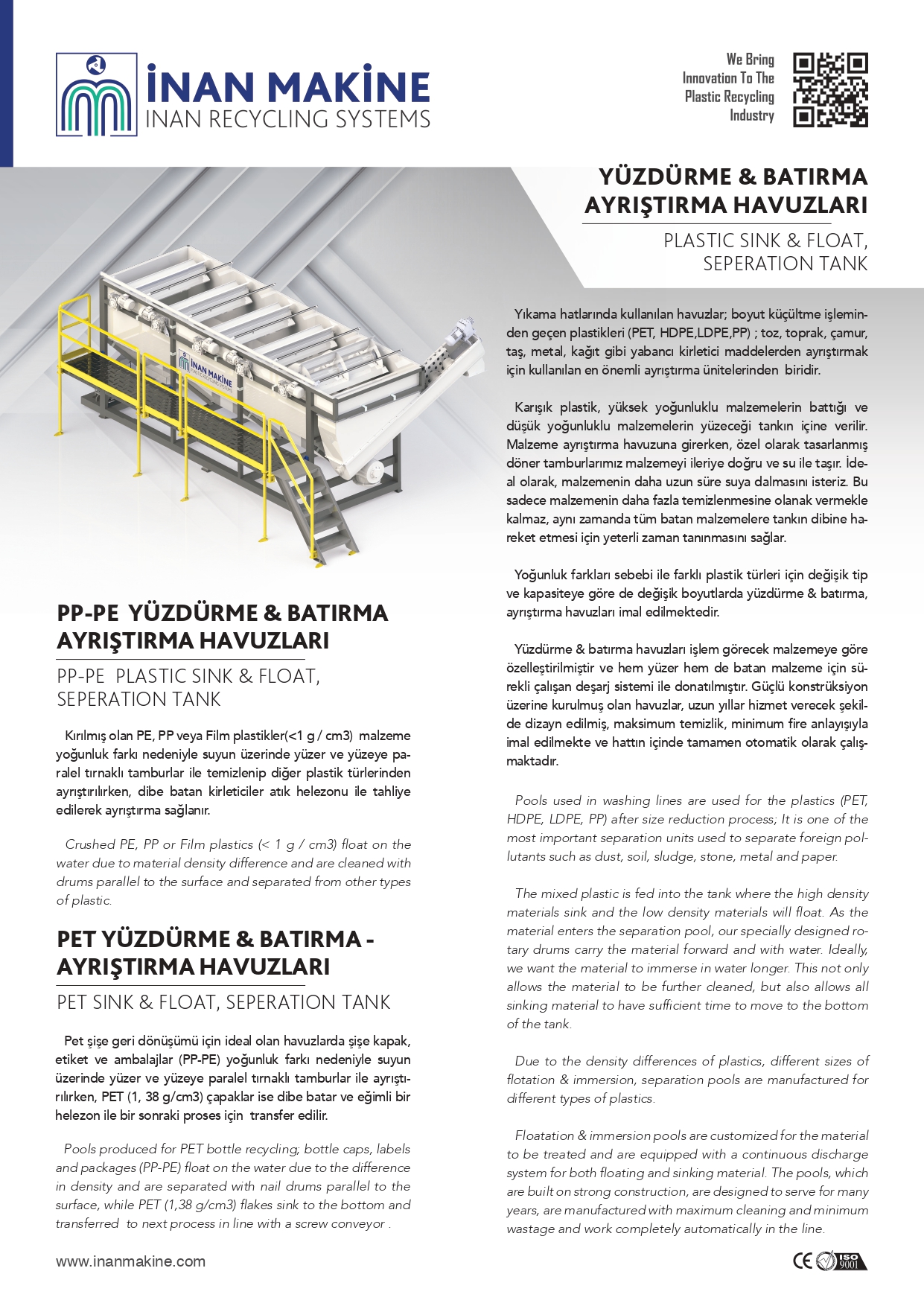
Pools used in washing lines are used for the plastics (PET, HDPE, LDPE, PP) after size reduction process; It is one of the most important separation units used to separate foreign pollutants such as dust, soil, sludge, stone, metal and paper. The mixed plastic is fed into the tank where the high density materials sink and the low density materials will float. As the material enters the separation pool, our specially designed rotary drums carry the material forward and with water. Ideally, we want the material to immerse in water longer. This not only allows the material to be further cleaned, but also allows all sinking material to have sufficient time to move to the bottom of the tank. Due to the density differences of plastics, different sizes of flotation & immersion, separation pools are manufactured for different types of plastics.
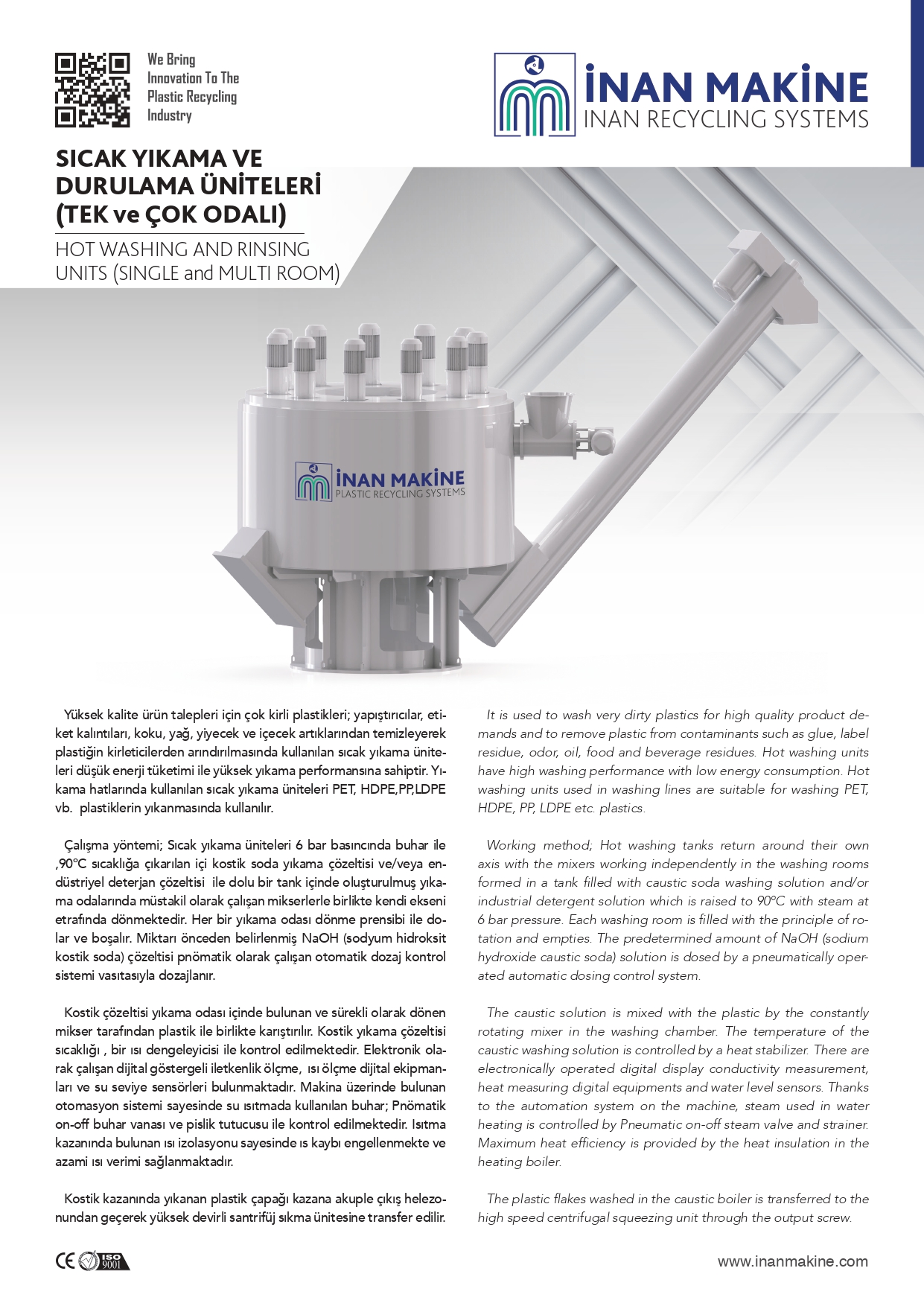
It is used to wash very dirty plastics for high quality product demands and to remove plastic from contaminants such as glue, label residue, odor, oil, food and beverage residues. Hot washing units have high washing performance with low energy consumption. Hot washing units used in washing lines are suitable for washing PET, HDPE, PP, LDPE etc. plastics. Working method; Hot washing tanks return around their own axis with the mixers working independently in the washing rooms formed in a tank filled with caustic soda washing solution and/or industrial detergent solution which is raised to 90ºC with steam at 6 bar pressure. Each washing room is filled with the principle of rotation and empties. The predetermined amount of NaOH (sodium hydroxide caustic soda) solution is dosed by a pneumatically operated automatic dosing control system.
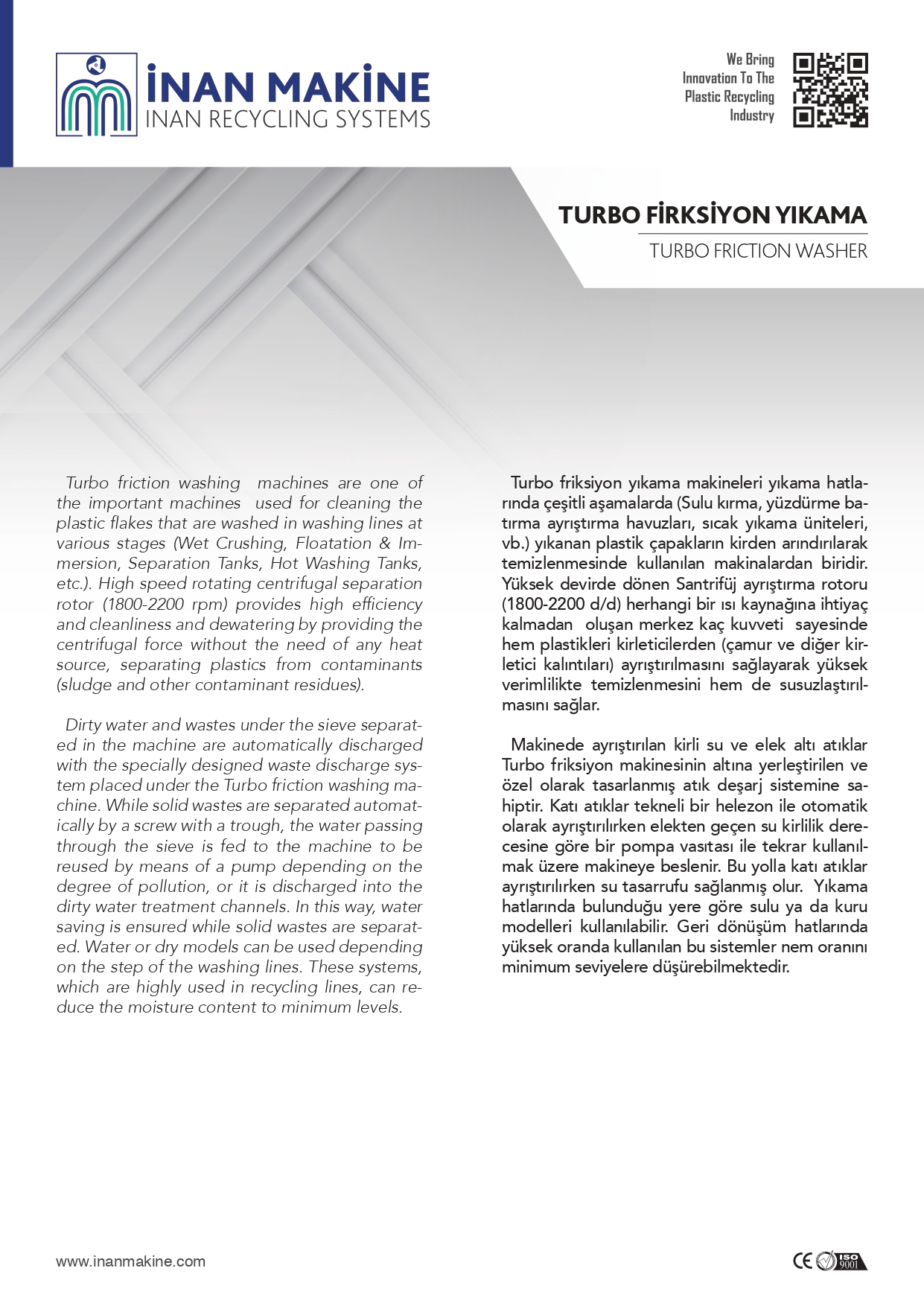
Turbo friction washing machines are one of the important machines used for cleaning the plastic flakes that are washed in washing lines at various stages (Wet Crushing, Floatation & Immersion, Separation Tanks, Hot Washing Tanks, etc.). High speed rotating centrifugal separation rotor (1800-2200 rpm) provides high efficiency and cleanliness and dewatering by providing the centrifugal force without the need of any heat source, separating plastics from contaminants (sludge and other contaminant residues). Dirty water and wastes under the sieve separated in the machine are automatically discharged with the specially designed waste discharge system placed under the Turbo friction washing machine. While solid wastes are separated automatically by a screw with a trough, the water passing through the sieve is fed to the machine to be reused by means of a pump depending on the degree of pollution, or it is discharged into the dirty water treatment channels. In this way, water saving is ensured while solid wastes are separated. Water or dry models can be used depending on the step of the washing lines. These systems, which are highly used in recycling lines, can reduce the moisture content to minimum levels.
Friction Washing washes dirty plastic materials under high speed (700 -1000 rpm) with pressurized water and provides deep cleaning with friction. Friction washing is used for cleaning both hard and soft plastic (nylon, bigbag). Thanks to the improved specially designed rotor and rotor blades, the friction is further enhanced and the efficiency of the centrifuge is increased. The screen placed inside the friction washing unit acts as a filter while separating the dirty water from the plastic. The dirty water is discharged by moving in the opposite direction and the plastic is transferred for the next process. It is used in washing lines for both product transfer and cleaning purposes. Friction washers are produced in different sizes according to the capacity.
Hot air pipe drying system is the last dryer commonly used in plastic recycling washing line. Suitable for most plastic materials such as PET, PP, PE, etc.(Rigid flakes). After dewatering, the plastic flakes are vacuumed by a fan and conveyed by stirring with hot air advancing along a long spiral set of stainless steel tubes. With the cyclone at the end of the pipeline, moisture is expelled. The spiral tube increases the contact area between plastic flakes and pipes. This increases the drying rate as the plastic flakes passes through the pipes with hot air and reduces the final moisture to international standards. Low consumption, high efficiency, anti-corrosion, excellent performance, make the pipe drying system an ideal equipment for plastic recycling production.
No represented companies found.
- İNAN GERİ DÖNÜŞÜM SİSTEMLERİ A.Ş.